5G is here, and mainstream adoption by industrial IoT startups is also coming
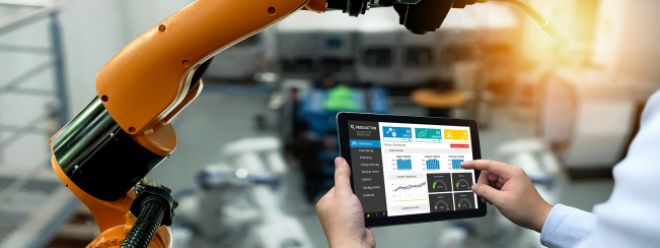
Since everyone is talking about 5G, it is equally important
to discuss the best potential of next-generation network bandwidth. To be
honest, Industry 4.0 is an upcoming trend until network troubles are resolved
with the emergence of private 5G networks.
Letting machines communicate with humans is a beauty called
the Internet of Things. The use of industrial machines for communication is a
breakthrough, perhaps the biggest breakthrough we know of. Since everyone is
talking about 5G, it is equally important to discuss the best potential of
next-generation network bandwidth. To be honest, Industry 4.0 is an upcoming
trend until network troubles are resolved with the emergence of private 5G
networks.
By 2026, they will reach $15.7 billion at a compound annual
growth rate of 79%, which is a huge number. Therefore, multiple industrial IoT
applications waiting for faster networks finally realized their best potential.
Why is 5G more suitable for industrial IoT?
Regardless of the fact that 4G networks have provided the
necessary beginning for the 4.0 revolution, now is the time to increase
strength and achieve a larger, better, and faster process on the ground. For
industrial IoT companies, 5G surpasses 4G; the latency of sending/receiving
data in 5G is 1 millisecond, while in 4G it is 200 milliseconds. Now, imagine
the changes in industries that work in highly agile environments such as
fast-moving consumer goods and healthcare. In addition, 5G can connect up to 1
million devices per 0.38 square mile. This is 100 times the number of 4G
devices, which is undoubtedly a boon for the unified dedicated network of
cross-location devices. Simply put, it can process more data at a faster speed,
but at a lower cost.
However, for the industry, this means more than just a fast
Internet.
The Operational Technology Suite (OT) in an industrial setting
uses a variety of fixed and mobile network technologies. In order to control
and communicate with equipment and floor processes, software applications must
transmit data in real time. For example, digital twins, automated production
lines, remote monitoring through real-time video, predictive maintenance, etc.
cannot be performed on ordinary networks. Their performance requirements are
high, and the usual Wi-Fi or LTE networks are not enough.
5G bandwidth is sufficient to support automated guided vehicles
(AGVs) with limited density. In order to upgrade production, it can support a
larger number of AGVs in each service area. Others, such as extended reality
headsets, are also making progress with the support of faster streaming.
Emergency equipment, also known as data goggles, can help maintenance engineers
understand complex industrial requirements in real time. It is not to be missed
that no matter how complex the industrial IoT environment is, it can ensure
remote control of equipment and processes around the clock.
For any enterprise, slicing is an indispensable strategy in
the network stack. Through virtualization, it is used to divide the incoming
network into multiple networks to satisfy different customers. In addition,
traffic from other networks will not affect the quality of service on a
particular slice. Just like tenants on the cloud platform, slices gain similar
exclusivity. 5G network slicing can enable or disable network fragments faster
and create on-demand subnets for specific departments in industrial settings.
5G is the dream of big data. Over the years, organizations
have established data management infrastructure to store, process, and stream
real-time analysis. Due to the close cooperation between the Internet of Things
and big data, 5G networks are a leading step towards edge computing. For the
industry, this is an emerging trend.
When we are doing it, the ubiquity of 5G private networks
should not be ignored.
Since most production units operate in different locations,
the network capacity of all units must be the same. For example, floLIVE
provides private 5G network solutions to support various use cases for small
and global enterprises. Therefore, whether it is a private campus network,
multiple campus networks in a country, or multinational services, their private
network solutions support multiple RAN providers. IoT solutions are built on a
software-defined connection (SDC) infrastructure to ensure flexibility and
security.
With pre-allocated IMSIs from the internal IMSI library,
companies can leverage multiple operators while creating a unified private
network for their companies. As a single dedicated network, their platform
simplifies the hassle of cross-border regulatory compliance. Cloud native
solutions emphasize performance and support strategies that comply with
enterprise verticals, employee security, enterprise security, and
confidentiality.
This solution solves a key network infrastructure challenge
facing the industry-centralized management of multiple sites and multiple
facilities through on-demand deployment options.
In Conclusion
Without remote and predictive data analysis, Industry 4.0 will
never be realized. The ability to track using process and performance sensors
and generate on-demand insights in real time is the foundation of what we call
smart industrialization today. All the other information you know about the
Industrial Internet of Things is related in one way or another. With the
development of technology, remote monitoring in the Industrial Internet of
Things will become mainstream like artificial intelligence. However, the
difference lies in controlling the quality of service of the device anytime,
anywhere.