Let’s talk about whether the presentation of operation and maintenance knowledge needs to be personalized?
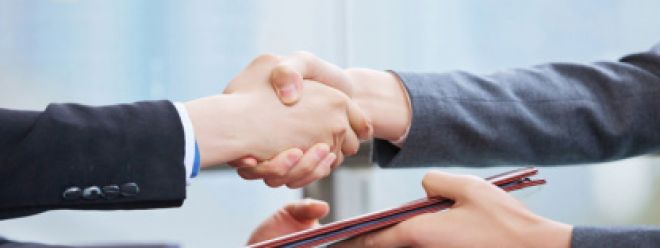
Over the years, various concepts have emerged in the field of database operation and maintenance tools. Each user seems to have his own special situation, and the functions of the operation and maintenance tools they need are also very different. Sometimes I feel a little confused about what users need. What kind of product is it. Some operation and maintenance tools are urgently needed by enterprises and are frequently used functions, such as database installation and deployment, automatic patching and upgrades, and batch modification of database configurations. With the construction of enterprise private clouds, these functions will gradually be included in the scope of cloud platform management.
As for the functions of operation and maintenance monitoring, system warning, system inspection, etc., everyone's needs vary greatly. We are engaged in the operation and maintenance knowledge automation system, and our goal is to help DBAs perform operation and maintenance monitoring, fault warning, root cause analysis, system inspection, SQL auditing, capacity management, security management, etc. by digitizing operation and maintenance knowledge. Digital operation and maintenance knowledge directly assists DBAs in their work, thereby reducing the cost of manual operation and maintenance.
Our product is very popular with some users and they feel that the tool is really helpful to them. For some users, they feel that they still trust the DBA's judgment more and still need to rely on the previous model to monitor and manage the database system. There are also some companies that have very strict controls. They have very strict requirements on how to monitor the system and even what commands to use. If the procedures are not followed and there is a problem with the system, the responsibility will be huge.
As the de facto product manager of D-SMART products, I often think about problems from the perspective of operation and maintenance personnel. How can "operation and maintenance knowledge automation" provide more help to front-line operation and maintenance personnel. An online communication with a customer two days ago gave me a lot of inspiration. Although this is just an expression of the needs of a certain user, I feel that the problems they encountered may still be representative. First of all, they recognized the concept of "operation and maintenance knowledge automation". They felt that they had bought many database operation and maintenance tools before, but they were just tools and did not buy the knowledge to operate and maintain databases. Therefore, these tools were used by them. The results are not very good, and most of them are no longer used after half a year after buying them. Our tool is something they think they can use for a long time.
However, although our tool concepts are relatively consistent with theirs, our tools currently cannot cover all of their daily operation and maintenance monitoring work, and some of their daily monitoring functions have not yet been covered. Later, I communicated with them some of their daily work. I found that actually some of the features in our tools were able to basically replace some of their previous monitoring behaviors. Because there are differences in some of our operation and maintenance concepts, some problems that we think can be solved through daily inspections require regular inspections every day. They are accustomed to using their own methods to analyze certain risks that we can assess in other ways.
In fact, everyone is using their own "operation and maintenance knowledge" to carry out daily operation and maintenance work. However, the operation and maintenance knowledge system is very complex. Although the operation and maintenance knowledge that everyone relies on daily is not contradictory from a theoretical basis, it is In actual work, people are more accustomed to monitoring and managing database systems according to their own habits. These differences in habits will still cause a lot of trouble for operation and maintenance personnel.
For example, a customer requires in their operation and maintenance manual to regularly collect the status of the listener on the server. Our tool does not have indicators for listening to detect the activity, but uses real connections to detect the availability of the database. In fact, our exploration includes the exploration of monitoring. If we can actually connect to the database, we must be sure that the monitoring is working normally, otherwise we will collect the message of monitoring failure. We can solve this problem by convincing users to accept our indicators, but for users, the best experience is to be able to directly see the indicator data of the monitoring status. In this case, there is no need to change their operation and maintenance habits. .
As developers of operation and maintenance tools, we cannot just consider the problem from the perspective of the tool and let users adapt to the characteristics of the tool. I even heard a friend from a tool manufacturer say that we need to educate users on their operation and maintenance habits. Let their operation and maintenance capabilities be improved. For some users, they may be able to fully accept a new monitoring work mode, but for some users, this may not be the case. In more than ten years of operation and maintenance work, they have accumulated some operation and maintenance experience that has been proven to be effective. It would also be a waste to completely discard it.
This is also a very important reason why large language models are sought after in the field of operation and maintenance, because it can answer your questions using the knowledge language system you are accustomed to, so that you do not need to make any knowledge system conversion. This feature is also what operation and maintenance tool manufacturers need to learn. Through simple configuration, personalized presentation of operation and maintenance knowledge is achieved, and the tool is as close as possible to the user's existing operation and maintenance habits. This not only allows users to use the tool faster and better, but also maximizes the role of the tool.
I readily accepted the customer's request and expressed that I would fully cooperate with them, incorporate all their daily operation and maintenance tool capabilities into the system as much as possible, and improve their monitoring without changing their existing operation and maintenance habits as much as possible. Early warning and fault analysis capabilities. Through communication, both parties felt that through this cooperation and using the basic capabilities of the existing platform, most daily operation and maintenance work can be made white-screened, and some operations can be further made screen-free.
To achieve this, they first need to automatically collect all their daily monitoring and inspection operations and allow them to view them conveniently through an integrated interface. Then gradually combine some analysis algorithms to automatically analyze these states and data to form a fault model that can be warned. Automatic warnings will be issued when certain types of abnormalities occur in the system. After a period of running-in, operation and maintenance personnel can develop a certain degree of trust in the system's early warnings. Then operation and maintenance personnel will not necessarily need to check the monitoring screen regularly in the future. Operation and maintenance work can also gradually change from white screen to screen-free. evolved.