Automotive Ethernet: Solve complex wiring harnesses and support more data
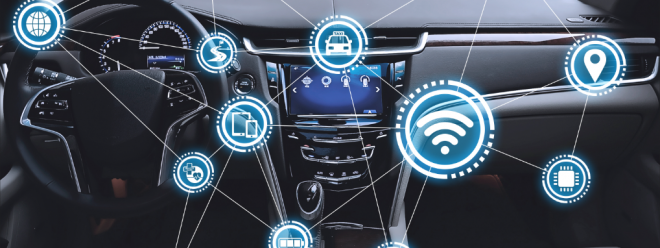
If you've ever had the chance to look at the tangled mess in a car's wiring harness, you know that these things can be quite large; hundreds of wires bundled together with zip ties that you'll hopefully never have to cut lest you scratch the sensitive parts inside. Shield.
These bundles take up valuable space within the car's chassis, add unnecessary weight and create more potential points of failure. But thanks to some new high-bandwidth cabling developed using enterprise-standard network protocols, this tangle of cables can be replaced with a single, slender wire that provides more bandwidth than all the other wires combined.
This is part of the promise of automotive Ethernet, but its benefits extend far beyond that.
Ethernet and the era of software-defined cars
The era of software-defined vehicles (SDV) is upon us. As more code runs more parts of more cars, it becomes increasingly possible to fundamentally change the way a car behaves or even drive using code downloaded from the cloud.
But more software running in a car also means more data. Lots and lots of data. All of these high-definition sensors that help modern cars understand the world around them produce a huge amount of information every second. All this data must be transmitted through the car in an endless stream of data that will soon become a river.
If that's not enough, you also get a modern infotainment system with 64 channels activated. Dolby Atmos audio or HD video is streamed to multiple rear-seat infotainment displays.
In other words, there's a lot going on under the skin of your next car, all of which requires more bandwidth. Ethernet is the solution.
What is Ethernet?
If you're familiar with the term Ethernet, you probably know that it's the cable (most commonly a Cat 6 Ethernet cable) used to connect your internet provider's modem to your wireless router. Or, if you're a serious gamer, you can use it to connect your PC or console directly to the network for the lowest possible latency.
This is a very common thing, but it's not exactly in-vehicle Ethernet we're talking about. Formally speaking, Ethernet is actually not a single type of cable at all; It is a networking standard that defines how multiple devices can interact safely and reliably.
By the way, Ethernet is capitalized because it refers to a technology registered by Xerox in the 1970s. Xerox issued the trademark so that the technology would eventually become a cross-industry standard, but it remains a proprietary name.
What we usually call an "Ethernet cable". Cables in your home contain multiple pairs of smaller cables inside, twisted together, which is why they are often called "twisted pairs." They usually have an RJ45 connector on each end, which looks like an oversized phone jack. The cable's official name is 100BASE-T or 1000BASE-T, which refers to data transfer speeds of 100 megabits or 1,000 megabits (gigabit) per second. If you're using Gigabit Ethernet, that should provide enough bandwidth to stream a 4K movie in about four minutes.
Even this is too slow when it comes to modern in-car data. Faster speeds require a completely different kind of cable. "We are talking about a technology called T1," said Amir Bar-Niv. He is vice president of marketing for Marvell Semiconductor Corporation, a major international semiconductor and networking equipment supplier headquartered in California. “Everything we do, 100 gigabit, gigabit, multi-gigabit and 25 gig, is designed for T1.”
When Bar-Niv says “25 gig,” he’s referring to 25G, which is enough for 8 seconds Stream the same 4K movies within a single device and have enough bandwidth for all the feature films you want.
The cable types here are not only optimized for speed, but also suitable for automotive use. It's thinner, lighter and cheaper than the clutter of cables behind your desk - a pair of wires twisted into a single cable, or even a fiber optic cable, using a new standard connector called T1 to deliver the next generation of SDV applications All the bandwidth required
is not always the case. In fact, automotive Ethernet dates back 15 years. "BMW first introduced this technology in 2008 on the F01 7 Series model," said Ian Richards, vice president of automotive operations at TechInsights, an international company specializing in semiconductor analysis. "It was initially used in diagnostic ports and also For 20mbps front/rear seat link on infotainment system. "The first applications used 100BASE-T cables, just like you would use in your home.
Of course, these evolving cable standards are a critical part of the system, but to actually build a network, you need a place to plug them in." On one end, you have sensors and systems that generate data and do the work. On the other end are the various processors in the car that process the data. Keeping everything moving in the right direction requires a series of network switching devices, namely switches and routers.
Putting these The switches are optimally placed within the car to minimize the amount of wiring required while still enabling all the devices in the car to communicate with each other. This configuration, often referred to as the network architecture or topology, is where things start to look interesting place.
Exit domain control
Traditionally, as a car gains features and options over its life, the bundle of electrical wiring, collectively known as the wiring harness, grows, with more wire looms being created with each new feature.
Barr-Neff says this is a legacy of an old way of connecting things, which he calls domain architecture.
Think of each system in the car (such as lighting or infotainment) as a separate domain. Each domain is directly controlled by one or more (perhaps dozens of independent microprocessing units), all dispersed throughout the car.
If the car gets some new features in a mid-life update, such as heated washer nozzles or a blind-spot monitoring system, more wires will be added to the bundle to control that feature.
“In a car where there is little or no sharing between domains, each domain needs to run all the cables around the car,” Bar-Neff said. "The result is, you know, a lot of cable, a high cost, a cable highway."
With Ethernet, he said, a car can be transformed into a collection of interconnected zones, each containing sensors or devices , which he calls agents: "Each zone now needs to have its own Ethernet switch connected to that All the proxies for that domain in the zone then aggregate all the traffic over a thin Ethernet cable that really forms the backbone of the car.”
In this way, multiple vehicle systems all communicate over the same network. Through sharing, the design of a car can be radically simplified. Instead of dozens of custom chiplets scattered throughout, there are fewer, more powerful CPUs handling all the digital heavy lifting throughout the vehicle.
In addition to simplification, this opens the door to the evolution of car behavior that is the hallmark of SDV. Bar-Niv points to automotive cameras as an example: "Today's cameras use point-to-point connections," he said, transmitting data directly from the imaging sensor to the system that uses it.
Because of this, the rearview camera can only be used as a rearview camera because other systems in the car cannot access it.
For example, cameras cannot be shared between infotainment systems and ADAS,” Bar-Neff said.
But once all of these cameras are communicating over Ethernet (all on the same network), software can be written to use the cameras in interesting new ways, such as turning a rearview camera into a dash cam that streams footage over the Internet. This feature can then be downloaded via an over-the-air (OTA) update.
This flexibility is at the heart of SDV, with 80% of new vehicles expected to move to this architecture by 2026, according to a recent survey of automakers, making it a $5.6 billion industry industry.
In other words: This isn't just a trend for high-end luxury cars.
And, as this trend continues, the need for more bandwidth will similarly increase. "100 megabits is sufficient for domain infrastructure. Now, anything less than 2.5 GB is unacceptable," Bar-Neff said.
Automotive grade reliability
Much of the core technology here is based on common enterprise network hardware—the same stuff banks or businesses use. However, its introduction into automotive applications requires greater reliability. If a piece of a bank's network hardware fails, the bank may incur losses until it is repaired. That's not great, but when a car's active safety systems run over a network, in the worst-case scenario, any failure could result in loss of life.
A key part of preventing such failures is improving the final quality of the components installed in the car. "We measure reliability using DPPM," Bar-Neff said, which stands for defective parts per million. Bar-Niv said that for consumer network equipment, DPPM is "in the range of a few hundred to 1,000."
In the automotive world, the goal is less than 1 DPPM, or one defective part per million produced.
But even if these parts are manufactured to higher standards, failures can still occur. This is where redundancy comes in, such as network switches that use so-called dual-core lockstep processors. Here, every calculation is handled by two processors. The output of each output is compared, and if there are differences, the algorithm can ensure that the entire system continues to operate based on the output of the functional processor.
Improve car safety
If every component in the car, from the high beams to the head-up display, was communicating on the same network, it sounds like a bit of a security risk. That's right. Previously, if a hacker gained access to a given system on a car (one of the domains we discussed above), it was less likely that the hacker could take over other aspects of the car's systems. Because of this inefficient amount of cabling, each system domain effectively runs on a separate, disconnected network.
In cars optimized to use automotive Ethernet, where everything is consolidated onto one network, the likelihood of system-wide access via a single compromised component is greater. Thankfully, the protection is also greater.
"What we need to prevent are so-called man-in-the-middle attacks," Bar-Neff said.
This refers to an attack in which a hacker effectively pretends to be an authorized system within a car, connects with other systems and uses them to access data within the car.
One way to thwart such attacks is to use hardware security modules (HSMs). They generate digital keys inside the vehicle, encrypting and digitally signing all data passed within the vehicle. This technology is typically only used in high-end enterprise digital networks, and its presence in cars ensures a similar degree of mobile security.
Costs and Benefits
Between the fancy cabling, switches, and HSMs, not to mention all the software that runs it all, running cars over Ethernet instead of the previous more basic but redundant domain model may sound like an expensive proposition.
"Yes and no," said TechInsight's Riches. “Yes, Ethernet costs more than the slower existing CAN links in vehicles. However, it is a fundamental building block for new vehicle architectures required to enable on-demand functionality and the high-speed communications required for autonomous driving.”
In other words, there is no way around this problem. Riches said Ethernet is "the only game in town" if you want to do things that require a lot of data. However, the cost of the network hardware to connect them will be miniscule compared to the cost of other sensors, such as the 3D laser scanner installed on the new Lotus Eletre.
In fact, in some cases, switching from a domain to a zone architecture, and removing all redundant components in the process, can actually save money. "There is also a long-term view that as computing performance becomes centralized, vehicle-level savings can be achieved by removing many of today's existing discrete ECUs," Riches said.
According to Bosch, a tier one supplier to many OEMs, switching to this architecture could reduce the cost of these in-vehicle networks by 10%. Future cars will also require 20% fewer in-vehicle components, such as microprocessors, according to Bosch, with ongoing shortages of such components still plaguing the industry.
So the move to automotive Ethernet could mean that cars will not only be smarter, cheaper, and lighter, but also less hard to find in the future.