How to deal with network equipment shortages
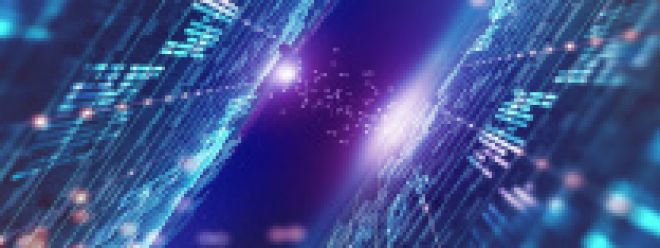
Today, delivery times are getting longer and patience is getting less and less. Here are some ways to deal with unprecedented supply chain disruptions.
Are people having trouble finding the necessary network equipment?
Device shortages are at record levels across nearly all network categories and device types. "The longest lead times appear to be larger, more complex equipment, such as data center and core/distribution switches, and large WAN edge equipment, including routers and SD- WAN equipment," said Mark Allen, director of Network Consulting Services, Global Technology Research and consulting firm ISG.
The main reason for the shortage is high demand for the chips inside almost all types of networking equipment. Shortages of these critical components are forcing businesses around the world to scale back their network upgrade and expansion plans due to the COVID-19 pandemic and surging demand for network equipment. All categories of network equipment are restricted: campuses, data centers, LANs, routing and wireless, said John Annand, director of infrastructure and operations research at IT market analysis firm Info-TechResearch Group.
Market research firm Gartner reported in mid-January that chip shortages are expected to ease in the second half of 2022, with global semiconductor revenue expected to grow 9.4% to $638.6 billion in 2022. Slower growth will follow in 2023 and 2024 as chip shortages diminish and prices stabilize.
This is certainly good news. For network equipment customers, however, the wait seems endless. Allen warned that given the current situation, businesses need to prepare for longer lead times, higher prices and stricter deal terms from OEMs and VARs.
fragile supply
While the chip shortage has affected a wide range of equipment customers, it has particularly hurt businesses building new networks, as well as organizations that have delayed equipment maintenance and updates, adopted just-in-time delivery models, or have yet to transition to cloud-native models. "Software allows us to reconfigure services running on the network with a great deal of flexibility, but if new or more ports are physically required, it's a bit of a no-brainer," Annand noted.
Annand said SMBs and businesses placing small orders were more likely to see longer lead times than larger organizations placing large orders to support large lifecycle projects or transformations. OEMs don't necessarily follow a first-in, first-out order model, focusing instead on fulfilling larger orders for more strategic customers.
preventive solution
There is no single best way for businesses to deal with shortages of network equipment, but with component lead times of 40 to 60 weeks, every business has to find a way, maybe even several, that works for them.
Annan made the following recommendations:
- Modify the network. There are many ways to build a network. If there were no parts in the initial design, perhaps a different approach, using equipment that was immediately in stock, could lead to similar results.
- Delay deployment. While some network deployments are fundamental, such as those in the core of a data center, others can be safely postponed. In situations where performance or functionality compromises are unacceptable, as unpleasant as it may be, latency may be the only option.
- Explore the secondary market. Some suppliers offer refurbished equipment directly or through partners.
- Increase density. Every network engineer knows there are dead ports and underutilized links in their environment - 10% to 25%, depending on who's numbers to trust, and need to get rid of them.
- Adopt cloud computing services. Public cloud services can provide at least minimal viable functionality for new or growing workloads. Even better, when network components become readily available again, it may no longer make sense to continue using the same amount of local footprint.
- Switch providers. Not all suppliers feel the pain equally, so it may be tempting to look for other sources. But keep in mind that switching vendors comes with compatibility, complexity, and support implications.
- Explore white box alternatives. Interest in white box networking has grown considerably over the past few years. For example, the use of a Linux-based network operating system breaks the dependencies between network functions and hardware vendors. "This allows you to get physical hardware from various OEMs at a lower cost," says Annand. However, the lower cost comes with increased engineering responsibility and accountability. "So you have to make sure your team is ready, and you're ready to invest and keep them," he warns.
- Increase spending. The law of supply and demand is alive and well. Companies that are willing to spend more on deals or strategy can expect a different experience dealing with device backlogs than those that remain in the status quo in 2020.
future outlook
Manufacturing plants take years to build. "Intel announced in May 2021 that the two plants are expected to be operational in 2024, so there is no obvious quick fix, and I don't think it's unreasonable to say that there will be supply constraints in 2023," Annand said.
Also keep in mind that future events may make the caught chip shortages tame in comparison.
In the short to medium term (six to 24 months), there shouldn't be any noticeable change in lead times for equipment, Annand said. As chip supply improves over time and supply chain issues are resolved post-pandemic, we expect longer lead times to start to ease.